CNC SERWIS Sp. z o.o.
Co oferuje CNC SERWIS?

Ambitny zespół serwisowy
Tworzymy wspaniały zespół fachowców. Regeneracja wrzecion jest naszym priorytetem. Firma działa nieprzerwanie od 2006 roku.

Uczciwość i jasne zasady naszych usług
Naszą zasadą jest uczciwość i przestrzeganie zasad Know How. Przestrzeganie tajemnicy służbowej to podstawa współpracy.

Opieka serwisowa
Pomagamy naszym Klientom w najtrudniejszych problemach związanych z elektrowrzecionami maszyn CNC

Współpraca
Na każdym etapie współpracy masz pewność iż zostaniesz dobrze potraktowany, a nasza współpraca będzie się rozwijać.
Serwisuj z nami

Nasza firma związana jest z naprawami maszyn CNC od zawsze.
Ciągły rozwój firmy i doskonalenie pracowników pozwoliło nam osiągnąć sukces. Elektrowrzecionami zajmujemy się od 2006 roku. Zaczynaliśmy w garażu o powierzchni 100 metrów kwadratowych i od kilku narzędzi. Dzisiaj nasz zakład liczy 12 osób i obsługujemy serwis wrzecion w Polsce jak i za granicą w takich Państwach jak Litwa, Łotwa, Wielka Brytania, Niemcy. Nasza firma rozrosła się do 1500 m2 przestrzeni użytkowej.
W swojej lokalizacji posiadamy maszyny i urządzenia takie jak obrabiarki CNC, szlifierki CNC, wyważarki, podstawowe maszyny manualne i urządzenia pomiarowe. Pozwala to na wykonywanie nawet najbardziej skomplikowanych remontów.
Serwis wrzeciona w naszej firmie ułatwi życie i ograniczy zbędne przestoje do minimum.
Zapraszamy do współpracy.
Regeneracja wrzecion i elektrowrzecion obrabiarek CNC

regeneracja wrzecion obrabiarek 5 osiowych
Naprawa wrzecion obrabiarek pięcioosiowych polega na przywróceniu wszystkich parametrów mechanicznych i elektrycznych do stanu producenta. Regeneracja wrzecion frezerskich ma na celu kompleksowy serwis. Serwis wrzecion frezerskich trwa zazwyczaj 7-14 dni
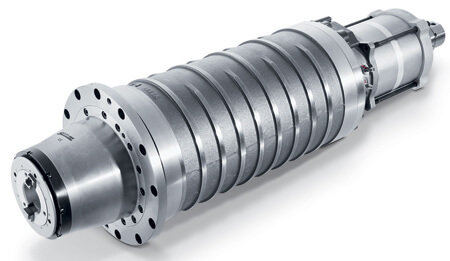
Regeneracja wrzecion frezarek
Naprawa elektrowrzecion polega na przywróceniu wszystkich parametrów mechanicznych i elektrycznych oraz sensoryki do stanu producenta. Regeneracja wrzeciona frezarki ma na celu kompleksowy serwis. Serwis wrzecion frezarskim trwa zazwyczaj 7-14 dni
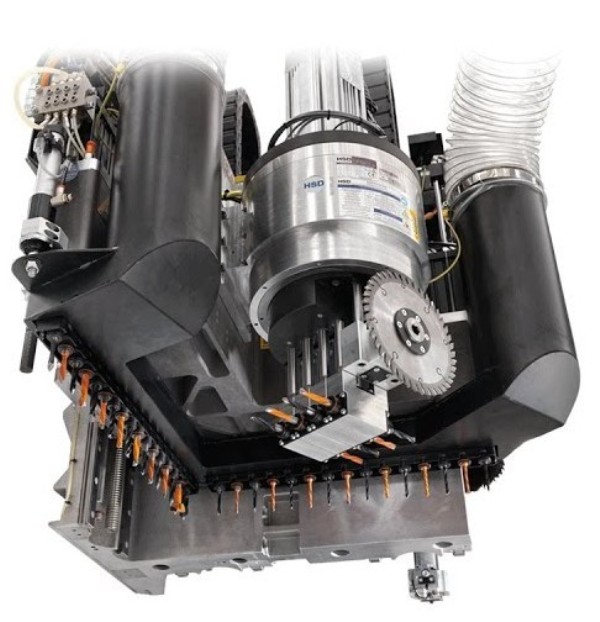
Naprawa głowic wielowrzecionowych
Naprawa głowic wielowrzecionowych polega na przywróceniu wszystkich parametrów mechanicznych i elektrycznych do stanu producenta. Serwis wrzecion ma na celu kompleksowy serwis. Serwis głowic wielowrzecionowych trwa zazwyczaj 7-14 dni
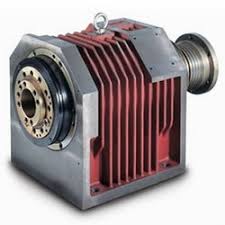
Regeneracja wrzecion tokarskicH
Naprawa wrzecion polega na przywróceniu wszystkich parametrów mechanicznych i elektrycznych do stanu producenta. Regeneracja wrzecion tokarskich ma na celu kompleksowy serwis. Serwis wrzecion tokarskich trwa zazwyczaj 7-14 dni
Usługi regeneracji wrzecion w firmie CNC SERWIS Sp. z o.o.
Serwis wrzecion – CNC SERWIS istnieje od 2006 roku i oferuje naprawę wrzecion wielu marek i producentów maszyn. Naprawa wrzecion polega na przywróceniu wszystkich parametrów funkcyjnych elektrowrzeciona doprowadzając do stanu producenta. Regeneracja wrzecion to proces naprawczy, który ma na celu przywrócenie pełnej funkcjonalności uszkodzonej części maszyny. Wrzeciono jest istotnym elementem wielu maszyn CNC, a jego uszkodzenie może przyczynić się do nieprawidłowego lub nieefektywnego działania całego urządzenia. Ważnym elementem w maszynie CNC jest sprawność podstawowego urządzenia obróbczego jakim jest elektrowrzeciono. Z ubiegiem lat naszej działalności dysponujemy coraz obszerniejszą dokumentacją techniczną do większości modeli elektrowrzecion, co umożliwia nam szybką i profesjonalną regenerację z zachowaniem oryginalnych parametrów przeprowadzanej naprawy. Posiadamy również duży magazyn łożysk precyzyjnych ceramicznych i stalowych od typoszeregu 7006 do 7016 oraz 7108 do 7116 w różnych tolerancjach, który jest niezbędny do przeprowadzenia szybkich napraw najczęściej spotykanych wrzecion na rynku europejskim. Dobór i posiadanie w magazynie odpowiednich łożysk o różnych tolerancjach jest podstawą prawidłowego wykonania każdej regeneracji albowiem jedynie odpowiednio dobrane łożyska zapewnią długotrwałą pracę wrzeciona. Nie stosujemy łożysk do parowania uniwersalnego z przypadkowymi tolerancjami. Stosujemy łożyska parowane przez producenta w procesie ich produkcji. Dysponujemy łożyskami NTN, FAG, SNR oraz specjalistycznymi o numerach kodowanych, tzw. chronionymi znakami producenta często niedostępnymi w handlu hurtowym.
Naprawa wrzeciona, zakres oraz co wchodzi w skład regeneracji elektrowrzecion
W skład naprawy wrzecion wchodzi wymiana sprężyn zacisku narzędzia oraz wymiana kompletu serwisowego łożysk wraz z tuleją podporową, Na zakończenie naprawy następuje wymiana i regulacja czujników zbliżeniowych odpowiedzianych za kontrole wszystkich mechanizmów oraz wyważenie dynamiczne i statyczne wszystkich elementów rotora w łożyskach własnych w klasie 0.4 G zgodnie z normą ISO 16084:2017
Serwis wrzecion trwa zazwyczaj kilka dni i odbywa się w naszych zakładach w Pomysku Małym k/ Bytowa.
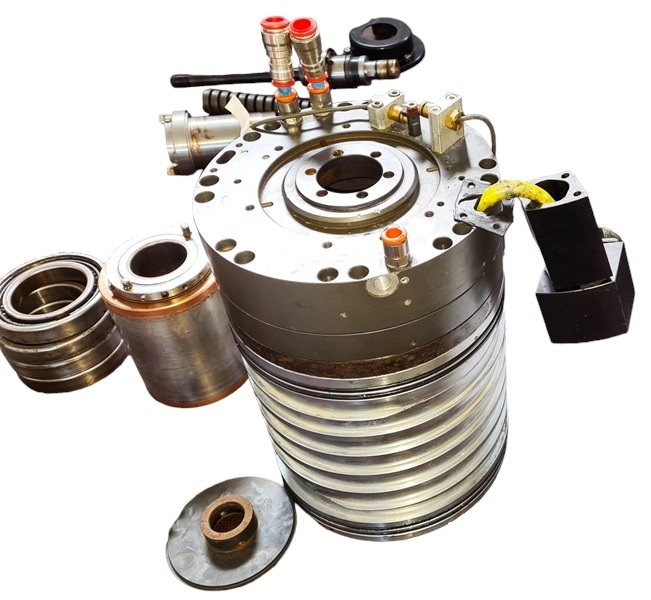
Każde regenerowane elektrowrzeciono jest rozkręcane, czyszczone a następnie poddawane szczegółowej analizie po której zostaje zweryfikowane pod kontem zakresu wymaganej regeneracji części składowych.
Przy bardzo wyeksploatowanych wrzecionach regeneracja wrzeciona polega na dorobieniu i odwzorowaniu elementów składowych tak aby wszystkie części zachowywały pierwotną użyteczność i właściwe wymiary oraz parametry techniczne.
Firma CNC Serwis Sp. z o.o. posiada wymagany sprzęt do regeneracji elektrowrzecion i wrzecion.
Wyważanie
Podczas regeneracji wrzeciona, czy elektrowrzeciona kluczowym zagadnieniem jest precyzyjne wyważenie dynamiczne wirnika przed instalacją łożysk jak i po niej w zainstalowanych już łożyskach własnych.
Elektrowrzeciono umieszczane jest w specjalistycznej wyważarce stacjonarnej CIMAT i napędzane napędem paskowych, następnie rozkręcane do właściwej prędkości obrotowej w celu uchwycenia punktu niedoważenia resztkowego i wkręcenia odpowiedniego odważnika określonego przez komputer. Czynność ta jest powtarzana do osiągnięcia określonej normy.
Nasza wyważarka wyważa z dokładnością 0,4 G w normie ISO 16084:2017. Jest to właściwa norma dotycząca regeneracji wrzecion wysokoobrotowych.
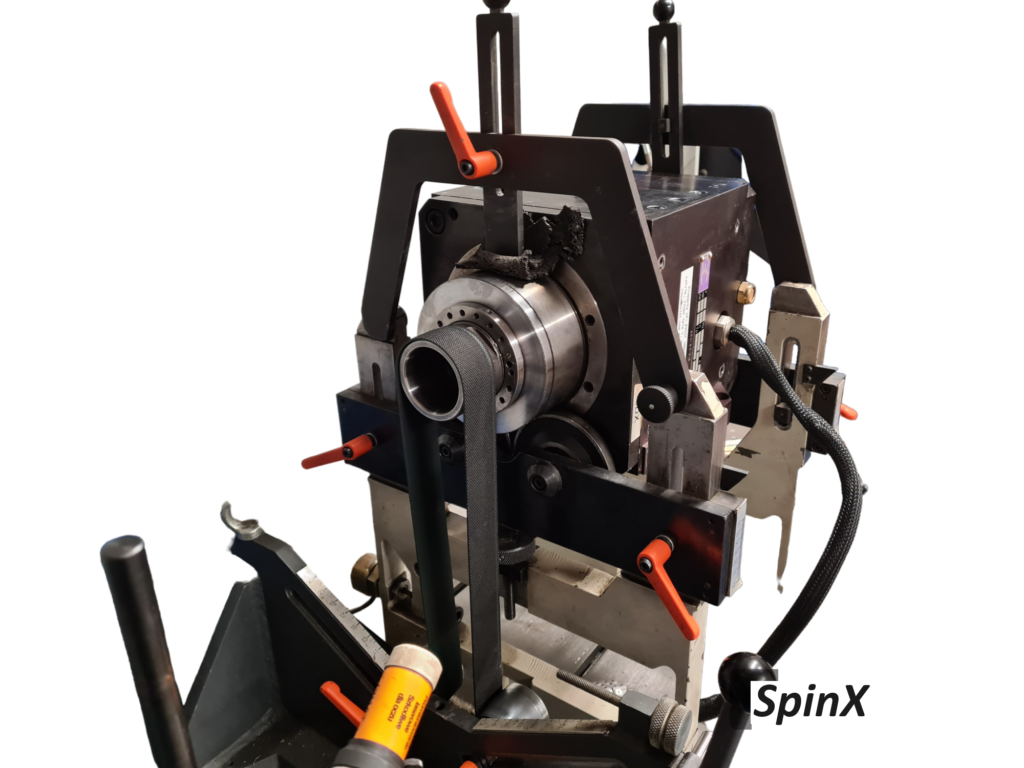
Łożyska wrzecionowe – wymiana i charakterystyka
Precyzyjne łożyska wrzecionowe standardowo składają się z pierścieni z bieżnią oraz z elementów tocznych w kształcie kulek ceramicznych bądź stalowych. Jest to również rodzaj skośny z bieżnią umiejscowioną pod kątem, którego kąt działania wynosi między 15 a 30 stopni. Kąt ma ogromny wpływ między innymi na nośność oraz sztywność zespołu łożysk i wrzeciona. Łożyska pracują w parach lub/i napinane są sprężynkami. Według specjalistów od łożysk optymalny kąt dla elektrowrzecion wysokoobrotowych do drewna wynosi 15 stopni (oznaczenie C) a do metalu 25 stopni (oznaczenie E). Regeneracja wrzecion wymaga ogromnej wiedzy w doborze odpowiednich łożysk. Ustawienie odpowiedniego napięcia wstępnego pary łożysk jest niezwykle istotne więc pozwól iż my się tym zajmiemy.
Co dają łożyska z kulkami ceramicznymi?
Po pierwsze są lżejsze od stalowych więc nie występuje tak duża siła odśrodkowa. Po drugie nie przewodzą, dzięki czemu prądy pochodzące z wirującego pola magnetycznego nie przechodzą z wirnika na stojan i odwrotnie. Wirnik jest galwanicznie odseparowany. W przypadku kulek stalowych prąd przechodzi przez przewodnik jakim jest stalowa kulka co ma ogromny wpływ na trwałość łożyska. Kulki stalowe się nagrzewają co ma ogromny wpływ na rozszerzanie łożyska pod wpływem temperatury. Łożyska ceramiczne uzyskują wyższe prędkości i są trwalsze, mniej się nagrzewają. W większości dzisiejszych konstrukcji wrzecion zastosowanie mają łożyska ceramiczne.
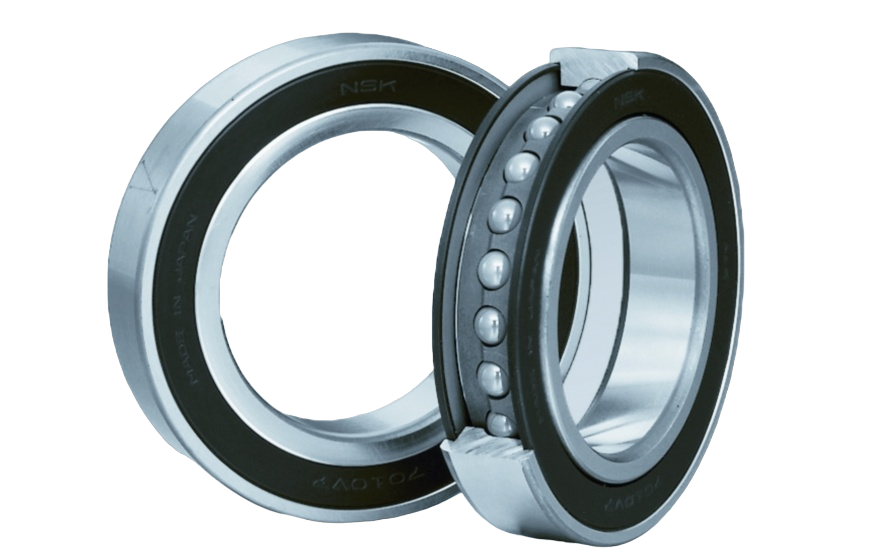
Łożyska wrzecionowe mają wiele zalet, a do głównych specjaliści zaliczają:
- trwałość
- niezawodność
- optymalna nośność podczas obciążeń
- możliwość pracy przy wysokich prędkościach obrotowych
- dokładność napięcia wstępnego
- odpowiednia sztywność i odporność na obciążenia
- precyzyjna geometria
Nasza firma korzysta wyłącznie ze sprawdzonych producentów wybierając najczęściej łożyska parowane. Wybierając markowe produkty otrzymujemy gwarancję długiej żywotności, ponieważ łożyska wrzecionowe produkowane są z wysokiej jakości materiałów. Oszczędzając na cenie łożysk precyzyjnych tracisz żywotność i ryzykujesz ponowną naprawą w krótkim czasie. Dobrze dobrany zespół łożysk wrzecionowych przy odpowiedniej eksploatacji będzie pracował lata. Z doświadczenia wiemy iż regenerowane przez nas wrzeciona pracują od 4 do 8 lat, w zależności od przepracowanych godzin. Serwis wrzecion wymaga ogromnego zaangażowania i wiedzy w doborze odpowiednich łożysk. Skorzystaj z pomocy specjalistów! Tutaj znajdziesz więcej informacji: https://spinx-group.com/naprawa-wrzecion/
Chwytak HSK F63 – serwis i ustawianie mechanizmu zaciągania
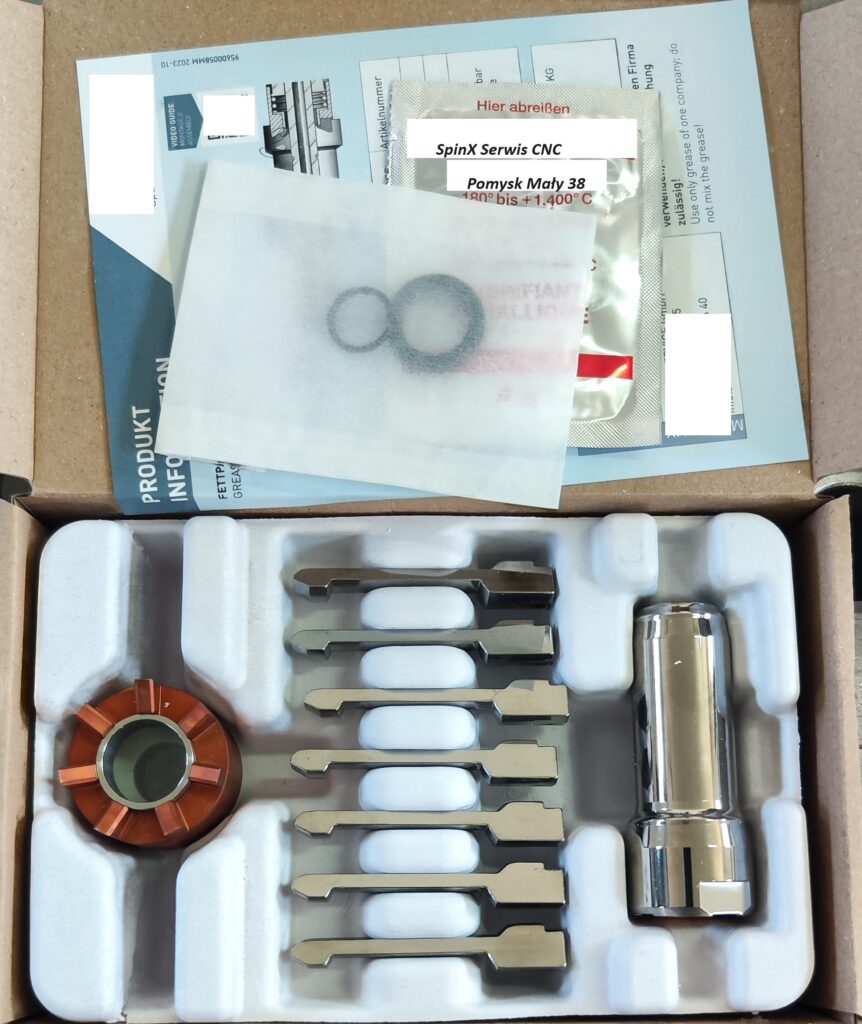
Regeneracja zaciągu wymiany narzędzia HSK 63F to ważny proces, który może pomóc w utrzymaniu wydajności i dokładności wrzeciona. Oto kilka kroków, które warto rozważyć:
- Sprawdź stan zespołu mocowania: Upewnij się, że zespół zaciskowy jest w dobrym stanie. Sprawdź, czy nie ma uszkodzeń, złamanych sprężyn lub innych problemów. Jeśli tak, wymień uszkodzone elementy.
- Smarowanie: Aby uzyskać odpowiednią siłę zacisku, zespół zaciskowy musi być dokładnie nasmarowany. Upewnij się, że wszystkie elementy są dobrze nasmarowane.
- Regulacja: Wyreguluj zespół zaciskowy. Upewnij się, że zaciąg nie ma złamanych sprężyn, a segmenty chwytaka są w dobrym stanie. Pamiętaj, że zespół chwytaka musi być odpowiednio wyregulowany.
- Wymiana zespołu mocowania: Jeśli zespół mocowania jest w złym stanie lub nie można go wyregulować, rozważ jego wymianę. Włóż pustą oprawkę narzędziową HSK-63F bez tulei zaciskowej do wrzeciona, aby zapobiec obracaniu się pręta. Następnie poluzuj śrubę blokującą i usuń uchwyt.
Jeśli musisz wymienić mechanizm zaciągu narzędzi skontaktuj się z naszym serwisem.
Dlaczego sposób naprawy, doświadczenie i zaangażowanie jest tak ważne?
Spółka CNC SERWIS Sp. z o.o. oferuje profesjonalny serwis wrzecion i elektrowrzecion obrabiarek. Serwisujemy i regenerujemy wrzeciona i elektrowrzeciona, które po naprawie nie odbiegają jakością oraz żywotnością od nowych maszyn. Firma posiada doświadczenie w branży CNC od 2006, a każdorazowy serwis wrzeciona jest przeprowadzany z indywidualnym zaangażowaniem i dbałością o szczegóły. Regenerowane wrzeciona oraz elektrowrzeciona są kompleksowo audytowane przez wyspecjalizowanych serwisantów którzy działają zespołowo. Dla potwierdzenia całkowitej sprawności oraz wyeliminowania niepotrzebnych przestojów maszyny każda naprawa wrzeciona czy elektrowrzeciona lub głowicy CNC jest objęta kontrolą jakości i gwarancją serwisową potwierdzoną odpowiednim protokołem serwisowym z wyszczególnieniem osiągniętych tolerancji geometrii wrzeciona lub elektrowrzeciona oraz sprawdzoną siłą zaciągu narzędzia. Firma oferuje całkowicie bezpłatną wycenę naprawy sprawdzanego elektrowrzeciona która trwa od 2 do 3 dni roboczych. Po oględzinach jest wykonywana kompleksowa oferta przez wykwalifikowanych specjalistów na podstawie przeglądu wrzeciona który ma na celu zlokalizowanie uszkodzonych elementów do wymiany czy regeneracji. Kosztorys przedstawiony po audycie zostaje zaakceptowany przez Prezesa Zarządu spółki , który szczegółowo przygląda się pracy serwisantów i podejmuje kluczowe decyzje w sprawie zakresu usługi, sposobu naprawy czy też ceny. Zachęcamy do podjęcia współpracy z wykwalifikowaną kadrą z dużym doświadczeniem. – Zespół przedsiębiorstwa CNC SERWIS Sp. z o.o. Sp.k – grupa SpinX.
Jaki jest koszt regeneracji?
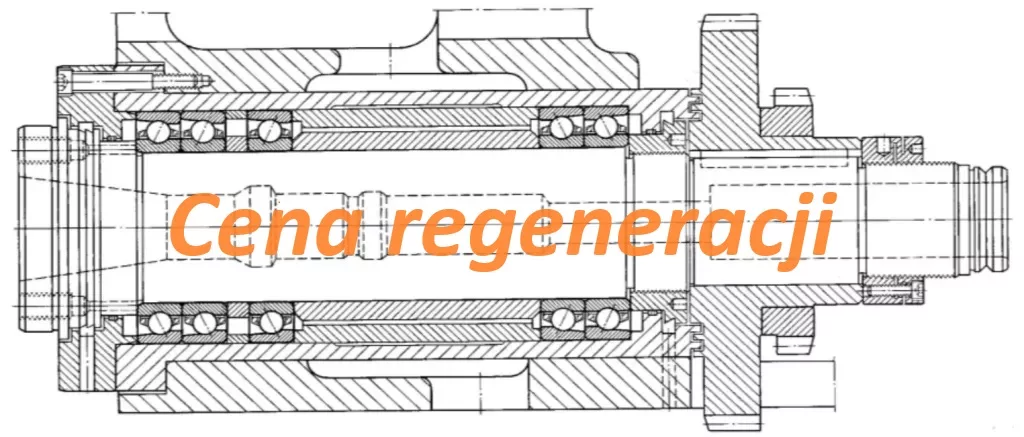
Koszt regeneracji wrzeciona i elektrowrzeciona zależy od wielu czynników, takich jak rodzaj wrzeciona, stopień uszkodzenia, wymagane części zamienne i wiele innych. Firma CNC Serwis oferuje regenerację wrzecion frezarskich w cenie od 12 000 do 18 000 zł netto z gwarancją na 6 miesięcy. Czas regeneracji wynosi zazwyczaj 5-14 dni roboczych, a w niektórych przypadkach gdy termin regeneracji nie jest krótki, na czas regeneracji udostępniana jest część zamienna.
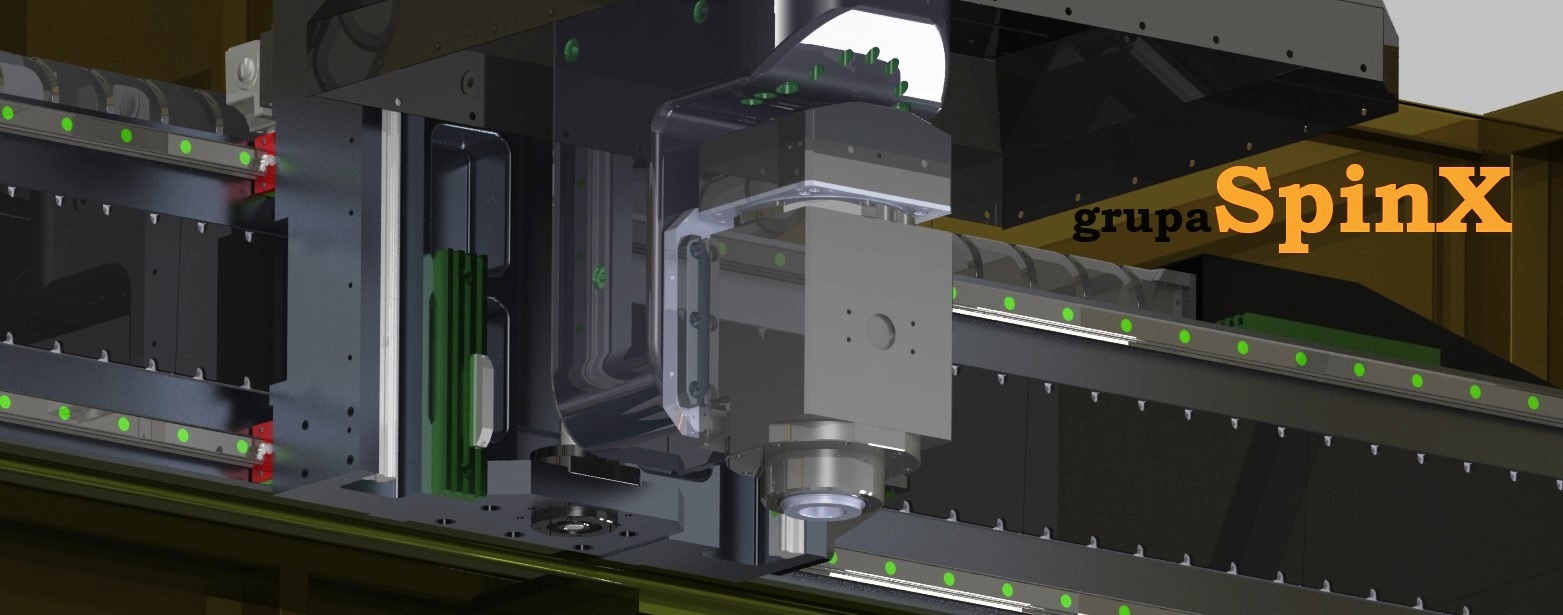
zarezerwuj usługę regeneracji wrzeciona
Tel (+48) 693-996-816
Naprawa wrzecion
Jakie wrzeciona regenerowaliśmy ostatnio?
Poniżej wybrane regeneracje elektrowrzecion w przedsiębiorstwie CNC SERWIS Sp. z o.o.
-
Regeneracja elektrowrzeciona StepTec
-
Regeneracja wrzeciona HARDINGE
Regeneracja wrzeciona HARDINGE już kolejna, Ponieważ wyspecjalizowaliśmy się w tym temacie od 2006 roku łatwo nam zregenerować każde wrzeciono tej firmy..
-
Naprawa głowicy CNC ELUMATEC
Demontaż i uruchomienie
Czy wiesz że zlecając nam regenerację elektrowrzeciona możesz liczyć na demontaż z maszyny i uruchomienie po naprawie?
Sporym problemem podczas zlecenia regeneracji elektrowrzeciona, jest brak świadomości iż wysłanie firmie urządzenia które nie jest demontowane przez ten sam serwis nie powoduje przelania odpowiedzialności za działanie całej maszyny firmie regenerującej wrzeciono.,
Bardzo często zgłaszają się do nas klienci którzy są niezadowoleni z poprzedniego serwisu, który wziął zapłatę jeszcze przed dostawą, a urządzenie pozostawiało wiele do życzenia. Po zamontowaniu urządzenia okazało się że działa tylko to co było wyszczególnione w ofercie. Po zamontowaniu w maszynie często wsparcia ze strony firmy regenerującej wrzeciono już niema. Dlatego też lepiej zlecić całość naprawy jednej firmie. Grupa SpinX podejmie się całości usługi.
Zakres napraw jaki zapewniamy to nie tylko warsztatowa regeneracja wrzeciona, ale też fachowe doradztwo, demontaż urządzenia z obrabiarki jak i jego uruchomienie po naprawie. Specjaliści grupy SpinX są technicznie doświadczeni i wykonują swoje zadania z pełną świadomością zakresu postawionych zadań. Ponieważ regeneracja wrzeciona i elektrowrzeciona to bardzo poważne przedsięwzięcie zleć naprawę wykwalifikowanemu zespołowi który umożliwi szybką i sprawną naprawę Twojego sprzętu. Jeśli masz problem ze swoją maszyną i podejrzewasz awarię wrzeciona lub jego podzespołów nie wahaj się skorzystać z naszej ogromnej w tym zakresie wiedzy.
Raport – regeneracja wrzecion
Warto zregenerować wrzeciono frezarki zanim będzie za późno!
Wprowadzenie:
Regeneracja wrzecion frezarek jest kluczowym procesem utrzymania wydajności i trwałości maszyn. W niniejszym raporcie omówimy znaczenie regeneracji wrzecion, techniki regeneracji oraz korzyści, jakie niesie ze sobą ten proces.
Jeżeli zauważysz iż wrzeciono głośniej pracuje lub ma wibracje albo się nagrzewa to już czas na serwis. Nie zwlekaj z tą decyzją, albowiem możesz doprowadzić do tak dużego uszkodzenia iż naprawa będzie bardzo kosztowna lub wrzeciona nie da się już zregenerować.
Znaczenie regeneracji wrzecion:
Serwis wrzecion jest niezbędny, aby przywrócić wydajność i precyzję działania frezarek. Przy regularnej eksploatacji wrzeciona ulegają zużyciu, a ich dokładność może się pogorszyć. Dlatego konieczna jest regeneracja wrzeciona, aby przywrócić oryginalne parametry techniczne i zapewnić prawidłowe działanie maszyny. Każde podejrzane działanie powinno być szybko wykryte. To zaoszczędzi ci czas i pieniądze.
Techniki regeneracji wrzecion:
- Czyszczenie: Usuwanie zanieczyszczeń, opiłków i innych substancji, które mogą negatywnie wpływać na działanie wrzecion.
- Wymiana łożysk: Uszkodzone łożyska są wymieniane, aby zapewnić prawidłowe działanie i wydajność wrzeciona.
- Wyważanie: Dokładne wyważenie wrzeciona pomaga w uniknięciu drgań i poprawia jakość obróbki.
- Naprawa osi: W przypadku uszkodzeń osi, przeprowadza się naprawę lub wymianę, aby przywrócić pełną funkcjonalność wrzeciona.
- Regeneracja stożka. Naprawa stożka wrzeciona polega na szlifowaniu stożka w celu uzyskania prawidłowej powierzchni i geometrii.
- Regulacja. Testowanie mechanizmu narzędzia jest jedną z najważniejszych powinności. Pomiar wysuwu trzpienia czy też siła zaciągu narzędzia powinny być na bieżąco sprawdzane. Dla uniknięcia awarii wrzeciona bądź bezpieczeństwa obsługi przynajmniej raz do roku obsługę techniczną powinno się zlecać serwisowi wrzecion.
Korzyści regeneracji wrzecion w odpowiednim czasie:
- Wydajność: Regeneracja wrzecion pomaga utrzymać wysoką wydajność maszyny, co przekłada się na efektywność procesów produkcyjnych.
- Trwałość: Naprawa wrzecion przyczynia się do zwiększenia trwałości wrzecion, co redukuje koszty związane z ich częstą wymianą.
- Dokładność: Przywrócenie oryginalnych parametrów technicznych wrzecion pozwala utrzymać wysoką precyzję obróbki.
- Oszczędność czasu i kosztów: Regeneracja jest zazwyczaj tańszą opcją niż zakup nowego wrzeciona, a także pozwala zaoszczędzić czas związany z dostawą i instalacją nowego komponentu.
Podsumowanie:
Regeneracja wrzecion frezarek jest nieodzowna dla utrzymania ich wydajności i trwałości. Dzięki różnym technikom regeneracji można przywrócić oryginalne parametry techniczne wrzecion, co przekłada się na oszczędność czasu i kosztów, a także poprawia efektywność procesów produkcyjnych. Pamiętaj o regularnym przeglądzie i konserwacji wrzecion, aby utrzymać ich działanie na najwyższym poziomie. Nie zwlekaj z decyzją o czasie naprawy. Jeśli zauważysz coś podejrzanego podczas obróbki natychmiast zatrzymaj maszynę i zleć sprawdzenie wrzeciona profesjonalnemu serwisowi.